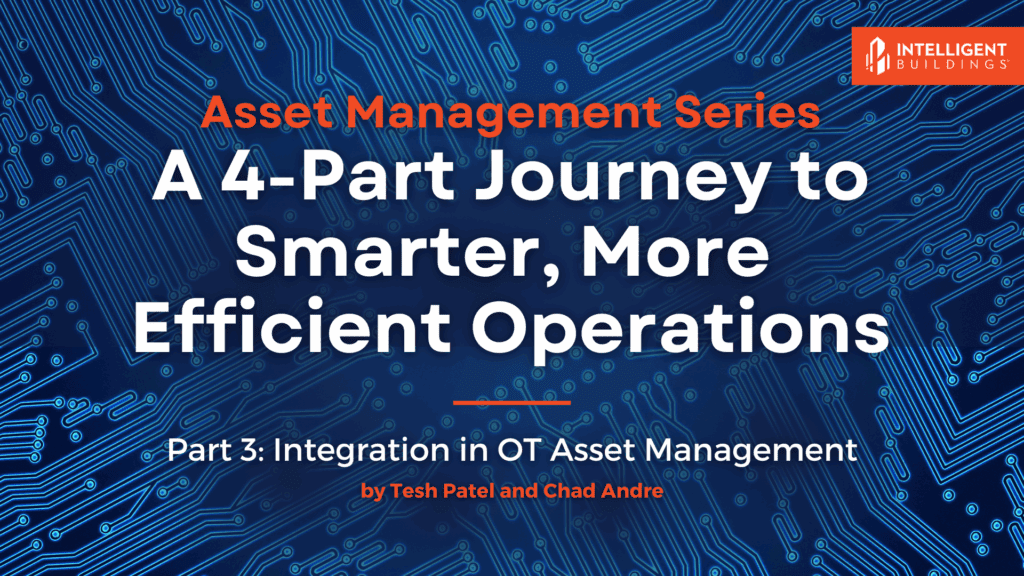
by Tesh Patel and Chad Andre
Asset Management Series
Did you miss Part 1 or 2? Check them out here:
Intelligent Buildings Website:
Part 1: Maximizing Efficiency in OT Asset Management
Part 2: Demystifying AI in OT Asset Management
LinkedIn Posts:
Part 1: Maximizing Efficiency in OT Asset Management
Part 2: Demystifying AI in OT Asset Management
PART 3 – Integration in OT Asset Management
Asset management depends on reliable data. Without it, even the best strategies fall apart. Yet many commercial buildings rely on a patchwork of disconnected operational technology (OT) systems: building management systems (BMS), computerized maintenance management systems (CMMS), energy platforms, vendor tools, spreadsheets, and more. These systems weren’t designed to work together, and that lack of integration creates friction, delays, and blind spots.
Integration, in the context of asset management, is about connecting those systems so that equipment data, maintenance history, performance metrics, and work orders are part of the same conversation. Done right, it improves visibility, reduces manual effort, and helps teams make better decisions about how assets are maintained, repaired, and replaced.
Why Integration Supports Better Asset Management
When asset data lives in separate systems, it often results in duplication, delay, or guesswork. Asset managers need a clear understanding of what equipment exists, how it’s performing, when it needs service, and how much it costs to maintain. When that information is spread across multiple systems, the result is delay, duplication, or guesswork.
Integrated systems help by:
- Bringing together asset performance and maintenance data
- Supporting condition-based maintenance instead of fixed schedules
- Creating more accurate reporting for capital planning
- Enabling faster action on equipment issues
Without integration, teams often work with incomplete or outdated information. With it, they can focus on planning, not chasing data.
How Integration Works in an Asset Management Workflow
- Inventory Accuracy: Integration helps maintain a consistent equipment list across systems. When an asset is updated or replaced in one system, it reflects everywhere else, preventing drift between operational teams and planning tools.
- Maintenance and Fault Tracking: When a piece of equipment goes into fault or begins trending toward failure, that signal can flow directly into the CMMS. Technicians see the fault and history, location, and any previous work in one place.
- Performance Visibility: Real-time energy use, runtime hours, and sensor data can be tied to the asset record, helping asset managers identify which equipment drives cost or risk.
- Capital Planning: Long-term asset decisions, such as repair vs. replace, retrofit timing, and equipment prioritization, are better when informed by consistent, integrated data over time.
Working with What You Already Have
Most portfolios don’t need to buy new systems to benefit from integration. The core platforms, BMS, CMMS, metering, and controls, are usually in place. What’s often missing is the ability to pass data between them in a structured, reliable way.
Asset management integration is less about adopting new tools and more about connecting existing ones through:
- Application programming interface (API) links or middleware platforms
- Standardized asset naming and tagging
- Shared references for equipment IDs, locations, and statuses
This approach keeps familiar workflows intact while improving how data moves between systems. It allows teams to build a more complete view of asset performance without introducing unnecessary changes.
Key Considerations Before You Start
- Data Governance: If two systems have different names for the same equipment, integration won’t work until that’s aligned. The foundation is a clean, structured asset list.
- System Ownership: Know who is responsible for maintaining each system and who has access to what data.
- Security: OT integration increases the surface area for cybersecurity risk. Segmentation, authentication, and regular review processes need to be in place from the beginning.
Putting It Into Practice
You don’t have to integrate everything at once. Start with a single use case, like linking fault detection data to your work order system or tying asset-level runtime to reporting dashboards. Keep the scope tight, track the results, and build from there.
When integration supports a specific need, getting buy-in, proving value, and scaling across the portfolio is easier. Over time, these connections form the foundation for a more proactive, data-informed approach to asset management, one that reduces manual effort, improves response time, and supports long-term planning with more confidence and less guesswork.